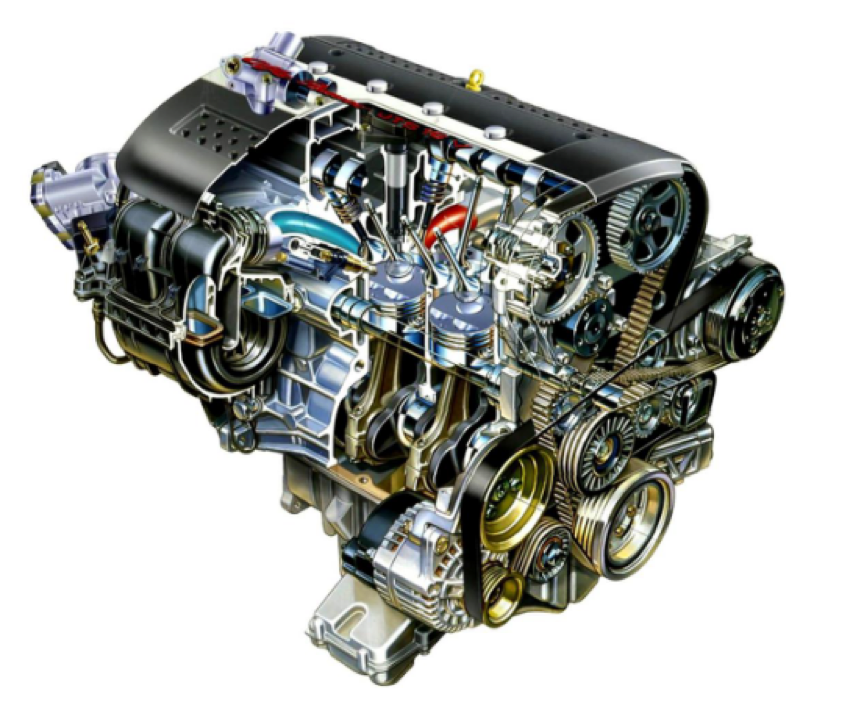
A Complete Guide to the History of Gasoline Direct Injection Technology – Become an Expert After Reading This! 🌟
Original by HonDa Magazine | Japanese Car Enthusiast Magazine | 2025-02-11 12:00:00
Gasoline Direct Injection (GDI) technology has been in existence for more than 95 years since its inception in 1925. Over this long development journey, many automobile manufacturers have explored its practicality and reliability—often learning valuable lessons from repeated failures. In today’s post, we take a systematic look at the evolution of GDI, with a special focus on how the technology has advanced since electronically controlled fuel injection became mainstream in the 1990s.
🌟 The Emergence of GDI Technology
🌟 Hello, my friend...
Welcome to a hidden gem—OLD FISHER DISCOUNT, your one-stop online shop with 9,999+ unique finds waiting for you. 🎉
🛒 Explore a World of Discoveries
Dive into our collection and uncover special treasures that will delight and inspire.
🔗 Start Your Journey Here: www.fisherdiscount.com
Come and see why we’re more than just a shop; we’re a place of endless possibilities! ✨
As the automotive industry expanded, the growing contradiction between increasing power demands and energy shortages became ever more apparent. In addition, the push for low-carbon, environmentally friendly solutions meant that even multi-point fuel injection systems could no longer satisfy consumer requirements. As the adage goes, “where there is demand, there is a market.” This need spurred the development of new, more precise injection technologies—giving rise to GDI.
Compared with conventional manifold fuel injection or carburetor systems, GDI engines eliminate the throttle valve. This design minimizes throttling and pumping losses while significantly improving intake efficiency. Instead of controlling engine speed indirectly via the throttle, modern GDI systems rely on the Engine Control Unit (ECU)/Engine Management System (EMS) to precisely adjust the fuel injection amount and timing 🔧. To achieve such precision, the EMS must boast robust storage and computing capacity—ensuring optimal ignition timing, power output, and driving performance.
Figure: Unlike traditional designs that mount fuel injectors in the intake manifold, GDI injectors are installed directly inside the cylinder. Fuel is injected with high pressure into the combustion chamber, achieving finer atomization and a more uniform air-fuel mixture for smoother, more efficient combustion. 💨
The positioning of the injector, the shape of its spray, the intake volume and pressure, and the design of the combustion chamber all influence the air-fuel mixture ratio. This flexibility allows the engine to operate in either homogeneous or stratified combustion modes.
Combustion Modes in GDI Engines
-
Lean Burn Mode:
Primarily used under light-load conditions such as cruising or deceleration, fuel is injected late in the compression stroke. This creates a small rich mixture near the spark plug—surrounded by lean air—to promote stratified combustion. This method minimizes heat loss and reduces emissions, as the stratified burn mainly occurs in the annular combustion chamber formed between the piston and cylinder head. 🔥 -
Stoichiometric Mode:
Designed for medium-load conditions, fuel is injected at the start of the intake stroke, promoting a uniform air-fuel mixture that ensures complete combustion and cleaner exhaust emissions. -
Full Power Mode:
For sudden acceleration and high-load conditions, the engine slightly enriches the air-fuel ratio (compared to stoichiometric mode) to prevent knocking. In this mode, injection begins during the intake stroke and may include multiple injections per cycle—such as a supplementary injection after ignition to boost power and fuel economy. Note that this extra injection can sometimes lead to incomplete combustion and potential exhaust valve damage, so manufacturers often disable it during normal operation.
Figure: Depending on the injector’s design and positioning, GDI technology can be classified into three injection modes:
• Spray-guided direct injection (e.g., used by BMW)
• Wall-guided direct injection (e.g., used in Ford's EcoBoost engines)
• Air-guided direct injection 😊
Early Development of Direct Injection (1925–1990s)
The world’s first gasoline engine with direct injection was introduced in 1925 by Swedish engineer Jonas Hesselman—the so-called Hesselman engine. Although this design proved the concept, it was not the true beginning of modern GDI.
-
1912: Archibald Low conducted the earliest test of gasoline direct injection on a motorcycle, verifying the technology’s feasibility but not moving toward industrialization.
- 1894: Diesel engines had already embraced direct injection, with prototypes dating back decades before gasoline applications emerged.
Hesselman’s approach involved lean-burn technology—injecting fuel at the end of the compression stroke and igniting it with a spark plug. Initially applied in gasoline engines, the method later evolved for diesel and kerosene engines. Hesselman engines, designed for low compression and using heavy fuel oil, were produced by Swedish truck companies such as Scania, Tidaholms Bruk, and Volvo until diesel technology eventually took over around 1936. 🚚
During World War II, GDI technology found military applications—most notably in aircraft engines like:
• Junkers Jumo 210 and Daimler-Benz DB 601 (Germany, 1937)
• Shvetsov ASh-82 FN (Soviet Union, 1943)
• Wright R-3350 (USA, 1944) ✈️
Figure: The 1937 Daimler-Benz DB 601 aircraft engine powered the legendary Messerschmitt Me109 fighter during World War II.
In early GDI systems, increasing engine power was challenging because fuel was injected only during the intake process. In traditional fuel injection engines, fuel could be delivered at any time during the four-stroke cycle prior to the intake valve closing. With direct injection confined to the intake phase, fuel quantity was limited—especially at higher engine speeds when injection time decreased.
Modern GDI systems overcome this limitation: injectors now generate enough pressure to allow injection even during the compression stroke, thereby extending injection throughout the entire cycle. To match the power output of conventional engines, GDI engines require higher-capacity injectors. Some manufacturers even combine direct injection with multi-point injection systems—for example, Toyota’s D-4S technology.
Figure: Toyota’s D-4S system employs two sets of injectors—one in the intake manifold for low-load efficiency and one in the cylinder for additional fuel under high-load conditions. 🛠️
The first automotive application of GDI was developed by Bosch and appeared in the Goliath and Gutbrod vehicles in 1952. By 1954, Mercedes-Benz introduced the 300SL Gullwing—the first sports car featuring GDI. This model used Bosch’s mechanical fuel pump and injectors, with the injector positioned in the cylinder wall alongside the spark plug—a design that later evolved in favor of indirect fuel injection due to cost considerations.
Figures:
• The 1952 Gutbrod Superior 700 Luxus was the first car with Bosch GDI technology.
• Its two-cylinder, two-stroke engine (663cc) produced 30 horsepower at 4,300 RPM—4 more than its carburetor counterpart.
• In 1953, Mercedes-Benz tested a new direct injection engine in the tenth 300SL race car (chassis number 0011/52), later known as the M198 engine used in the 300SL Gullwing. 🚗
The Transition to Modern GDI (1970s–Present)
Early Electronic and Experimental Systems
- Early 1970s: American Motors Corporation (AMC) developed a continuous fuel injection system (SCFI) for its redesigned straight-six engine. Unlike conventional systems, SCFI relied solely on measuring incoming airflow for fuel injection control. Although the “Straticharge” engine was road-tested in the 1973 AMC Hornet, inherent fuel supply issues prevented widespread adoption.
-
Late 1970s: Ford introduced the ProCo (Programmed Combustion) system with stratified combustion technology in its V8 engine used in the Ford 115 and Crown Victoria. However, high pump and injector costs, immature electronic controls, and excessive NOx emissions (in violation of upcoming EPA standards) led to the program’s cancellation.
Figure: The 1983 Crown Victoria featured ProCo stratified combustion technology—an ultimately flawed system that was soon discontinued. 😕
Following the 1970s oil crisis, manufacturers increasingly focused on fuel economy, leading to the widespread adoption of mechanical and electronically controlled multi-point fuel injection systems. By the mid-1980s, computer-managed electronic fuel injection became the norm, paving the way for modern GDI engines.
Mass Production of GDI Engines
- 1996: Mitsubishi launched its first electronically controlled GDI engine, the 4G93, in the eighth-generation Galant. Despite mixed reception in Europe due to lower power output and high-sulfur fuel issues, Mitsubishi continued refining its technology—producing over one million GDI engines by 2001.
- 1997: Nissan introduced its GDI system with NEO Di technology on the VQ30DD engine in the Leopard. Capable of delivering 230 horsepower and 294 Nm of torque, NEO Di featured innovative NEXT combustion (for precise control over fuel mist and combustion mode) and NTD control (adjusting torque based on throttle input). In 2010, Nissan rebranded this system as DIG.
-
1998: Toyota debuted its D-4 direct injection system on the 3S-FSE engine in the 11th-generation Corona. For the European market, the 2001 Avensis with the 1AZ-FSE engine was the first to adopt this technology. Later, Toyota’s 2GR-FSE V6 engine evolved into the D-4S system, combining direct and port injection for optimal performance and fuel economy.
-
1999: Renault launched its 2.0L IDE (Injection Directe Essence) system on the Megane, using recirculated exhaust gas (EGR) and concentrated fuel injection near the spark plug to improve low-load fuel economy. Later refinements targeted high-performance engines.
- 1999: The French PSA Group (Peugeot and Citroën), along with Hyundai and Volvo, introduced GDI engines based on Mitsubishi’s technology. The PSA Group’s system, known as HPi, powered the Citroën C5 and Peugeot 406 in 2000, delivering 140 horsepower from a 2.0L 16-valve engine.
-
2000: Volkswagen introduced its FSI (Fuel Stratified Injection) system in the Lupo—a 1.4L naturally aspirated engine producing 105 horsepower. Derived partly from racing prototypes, FSI improved fuel consumption by 30% (down to 4.9L/100km) compared with non-GDI versions. The technology was later applied to Volkswagen’s 2.0L TFSI engines.
-
2002: Alfa Romeo licensed GDI technology under the name JTS (Jet Thrust Stoichiometric), first seen on the 156. JTS employed dual-phase injection to achieve stratified combustion at low RPM (below 1,500) and a single injection at higher speeds to reduce NOx emissions.
-
2003: Honda developed its own GDI system—i-VTEC i—based on stratified combustion, debuting in the K20B engine (used in the 2003 Stream Absolute). Although the K20B was discontinued in 2007, its evolution paved the way for Honda’s later Earth Dreams Technology.
- 2003: BMW introduced its first GDI system on the N73 V12 engine. Later, BMW refined the system into HPI (High Precision Injection) with piezo injectors—first appearing on the 2006 N54 turbocharged inline-six. BMW then collaborated with PSA Group on new engines featuring HPI, as seen in the 2007 MINI Cooper S.
-
2003: Ford launched its GDI engine, the Duratec SCi (Smart Charge Injection), on the 1.8L Mondeo. This system—featuring piezo injectors and DISI technology—was Ford’s first GDI offering in Europe. Ford later expanded its portfolio with the EcoBoost family (including turbocharged GTDI engines), debuting a 2.0L version in the 2008 Explorer. EcoBoost engines use specially designed pistons with curved tops to generate vortices for improved air-fuel mixing and lean burn even at low speeds.
-
2003–2007: General Motors introduced several GDI engines. Starting with a 2.2L Ecotec engine (155 horsepower) for the Opel/Vauxhall Vectra and Signum, GM later launched turbocharged versions (e.g., the 2.0L Ecotec LNF) and the 3.6L V6 LLT engine for Cadillac. Subsequent models included the 2.4L LAF and later Ecotec variants.
-
2005: Mazda rolled out its DISI (Direct Injection Spark Ignition) system in the Mazda 6, later implementing it in the CX-7 and Mazda 3 for global markets. DISI ensures thorough air-fuel mixing and reduced cylinder temperatures (thanks to the heat absorption during fuel atomization), enabling higher compression ratios and improved efficiency.
- 2006: Mercedes-Benz introduced CGI (Charged Gasoline Injection) in the CLS 350 CGI. With piezo injectors, CGI decoupled fuel delivery from the intake valve and piston, enabling Ultra Lean Burn mode (with air-fuel ratios as high as 65:1) under light loads. The system boosted output by 20 horsepower (totaling 295 horsepower) while enhancing fuel economy and reducing CO₂ emissions.
- 2009: Ferrari debuted its first GDI-equipped car, the California (F149), followed by the 458 Italia—the first mid-engine Ferrari with GDI. Developed jointly with Bosch, Ferrari’s system featured independent injection for each cylinder. The 4.3L V8 (F136 IB) produced 460 horsepower at 7,750 RPM and 49.49 kg-m of torque at 5,000 RPM, achieving an impressive specific output of 107 PS/L. Porsche also introduced GDI in its 997 and Cayman models that same year.
-
2012: Subaru adopted GDI technology in its FA20 DIT (Direct Injection Turbo) engine, which features AVCS (Active Valve Control System) and a turbocharger. This engine, used in models like the Legacy, Levorg, and WRX S4, delivers up to 300 horsepower.
Figure: Subaru’s FA20 DIT engine as seen in models like the WRX S4 and Levorg. 🚀
Conclusion
With the continuous advancement of electronic management systems and the reduction in component costs, GDI technology has become increasingly prevalent among automakers. It offers notable advantages in terms of fuel efficiency, power output, and precise combustion control. However, it is not without drawbacks:
- Valve Carbon Buildup: Nearly all single-injector GDI systems are prone to carbon deposits on the valves.
- Higher PM2.5 Emissions: Compared to traditional multi-point injection systems, GDI engines typically produce higher particulate matter.
-
Increased Noise and Maintenance Costs: GDI engines can be louder and may require extra noise insulation, leading to higher maintenance expenses and reduced long-term reliability.
While GDI technology represents a significant leap forward in engine performance and efficiency, it is not a panacea for all the challenges associated with gasoline engines. As the debate over fossil fuel depletion evolves, automotive engineers may well revisit and refine the role of GDI in future engine designs. ✨
Leave a comment